継続的な人材教育で強い現場づくりを目指す
株式会社アイシン様
継続的な人材教育で強い現場づくりを目指す
~「PM分析教育」は、生産現場の技能を支える屋台骨~
そのような同社においてJMACは15年以上にわたり人材育成に関わらせていただき、中でも製造現場の人材育成においては10年以上にわたって支援させていただいています。
今回は同社の製品の根幹を担う「製造現場の人材育成」、特にJMACが長年継続して関わらせていただいている「PM分析教育」を中心にその背景や教育体制、役割についてお話を伺いました。
1965年設立
・本社所在地 〒448-8650 愛知県刈谷市朝日町二丁目1番地
・事業内容 自動車部品、エネルギー・住生活関連製品の製造販売
・従業員数 単独 35,610人 連結 約116,649人(2023年3月31日現在)
インタビュー:株式会社アイシン
TQM推進部 業務品質改善室 グループ長 角谷 幹彦氏(写真 右)
TQM推進部 業務品質改善室 主幹技術員 西雪 信太朗氏(写真 左)
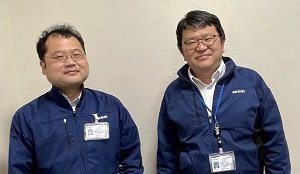
インタビュアー:株式会社日本能率協会コンサルティング
顧問・マスターTPMコンサルタント 和泉 高雄(写真 左)
プロフェッショナルプランナー 肆矢 勝彦(写真 右)
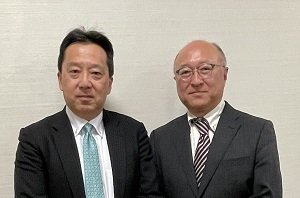
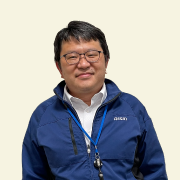
■TQM推進部 業務品質改善室
グループ長 角谷 幹彦氏 プロフィール:株式会社アイシン
1990年 アイシン精機株式会社(現 株式会社アイシン)に入社
駆動技術部に配属 クラッチの実験・解析、設計を経験
2003年 TQM・PM推進室(現 TQM推進部)に異動
TPM推進に関わり、現在はデータ活用推進業務に携わっている。
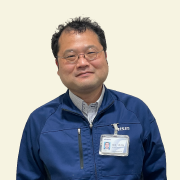
■TQM推進部 業務品質改善室
主幹技術員 西雪 信太朗氏 プロフィール:株式会社アイシン
2004年 アイシン精機株式会社(現 株式会社アイシン)に入社
TQM・PM推進室(現 TQM推進部)に配属
入社以来、TPM推進に関わり、現在は良品条件マネジメントのグループでの普及に携わっている。
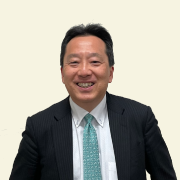
■和泉 高雄 プロフィール:JMAC顧問・マスターTPMコンサルタント
全日本能率連盟認定マスターマネジメントコンサルタント・国際公認経営コンサルティング協会認定コンサルタント、TPM優秀賞審査員、早稲田大学理工学術院非常勤講師
1984年(社)日本能率協会・(社)日本プラントメンテナンス協会に入職、以降TPMの普及、コンサルティング、TPM賞の審査に従事、2005年分社化、2013年グループ再編を経て日本能率協会コンサルティング取締役、2019年より現職。これまでの支援・審査企業は100社以上
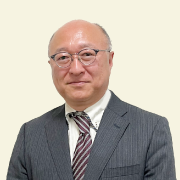
■肆矢 勝彦 プロフィール:JMAC プロフェッショナル・コンサルティングプランナー
1992年 (社)日本プラントメンテナンス協会に入職。地域担当として、TPMの普及、セミナー、研究会の企画・運営、コンサルティング支援やTPM優秀賞事務局を通して、その発展に尽力する。2013年グループ再編を経て日本能率協会コンサルティングに入社、顧客目線に立ったコンサルティングメニュー作成や社内教育立案、時流に合ったアンケート調査等々を行ない、いかにしてご支援する企業が半歩先を行けるかを念頭に提案している。
TQM推進部 業務品質改善室 主幹技術員 西雪 信太朗氏(以下敬称略):
まだアイシン精機時代の話になりますが、当社では、最初にQCサークル活動を1965年に導入しました。その後1970年にTPS(トヨタ生産方式)を始めています。
その後、当社ではV85というビジョン経営を掲げまして、そこの基本方針で品質と生産性を高めるためにTPMを開始しました。日本品質管理賞を受賞した際の指摘事項もありまして、その後設備管理の強化を図っていったのです。その時に同じ取り組むのであれば賞取得を目指そうということで、次にPM賞受賞を目標におきました。当時まだTPMの8本柱という活動が主流になる前だったのですが、当社では5本柱を掲げて活動していました。
先輩等から口伝えで聞いた活動ですので、明確に正しいかどうかわからないのですが、初めて品質保全と言う言葉を使い、賞取得の際に取り組んだと聞いています。このように品質とTPMというのが非常に親和性の高い形で活動が進んでいきました。
JMACマスターTPMコンサルタント 和泉 高雄(以下、JMAC):
デミング賞を1972年、日本品質管理賞を1977年、TPM優秀賞を1982年、そしてTPM優秀特別賞を1985年に受賞され、日本で初の4冠を達成されました。
西雪:
はい。当社では賞取得から一段落して、TPM活動が若干下火になっていたのも事実です。
そんな中、1997年に刈谷工場で火災が発生しました。PM賞を取った会社がなぜ火事など起こすんだとそれは大変お叱りを受けました。そして、賞取りに目標をおいた活動ではなく、TPMの本質に立ち戻った活動に取り組むように厳命されたのです。当時、設備のところでも木製の板等を使っていまして、クーラント液が染みたりして大変な状態でした。それを鉄板に変えたり、可燃物の除去や5Sに取り組んだり、本来のPMの基礎中の基礎からやりなおしが必要と判断しました。
JMAC:
一斉対応で大変だったと伺っております。
西雪:
その後、自主保全をスタートさせます。
以前からJIPM(公益社団法人日本プラントメンテナンス協会)の研究会などに参加し、他社との交流も行ってきました。その中でまずは和泉先生も企画メンバーであったと聞いています自主保全士の資格から取り組み始めました。生産保全技術研究所やJIPM、JIIPMソリューション(現JMAC)の支援がスタートしたのは、2006年でした。
専門保全ではなく、生産保全の方に入るところからだと記憶しています。5Sの活動はすごくお金のかかることだったので、当時はいろいろ足りないところがあれば費用をかけて大規模にやっていたのですが、長く活動を継続するとなると、そんなことばかり言っていられません。ではどうやって続けていけばいいかと考えた時に、会社として儲けながらでないと活動ができないんじゃないかと言う話になりました。そんな中で「ロス」と言う言葉にスポットが当たっていったのです。
JMAC:
TPMの本質であるロスの検出力向上とその撲滅に比重を置かれたわけですね。
TQM推進部 業務品質改善室 グループ長 角谷 幹彦氏(以下敬称略):
まず、どのくらいラインにロスがあるんだろうと言うことで検証を始めました。そうやってロス改善に取り組んでいけば、ロスを低減させることで結果として会社の利益につながり、活動を継続できるんじゃないかということになったのです。
西雪:
当時は生産技術と共同事務局で実施していたんです。そこで、見つかったロスに対してどう対応しようかと言うことで指導会を立ち上げたのです。この指導会をやっていく中でロスと言う観点がとても良く、いろんな工場で成果を上げました。新豊工場、西尾ダイカスト工場など最初に入れた工場があったのですが、このように指導会を通してロス低減として大きな成果を上げることができました。
JMAC:
強制的な運動から成果が生まれ、自発的な活動へと変化発展したわけですね。
西雪:
そんな中、加工点が特にクローズアップされていきました。加工点研究からの良品条件作りといった活動についてですが、加工点の原理原則、良品条件の設定等これ自体が新しいものでは無いのですが、加工点解析の中に良品条件を取り入れたのは、当社オリジナルに近いと思います。もともと良品条件に加工点解析を入れた経緯は、当時の副社長から、グループとして取り組んでいる良品条件というものがあるから、活動の中でやってみてはどうかということになりまして。では加工点解析だったらできますと言う話になり、急遽テキストを作って実践してきました。
もともと加工点と言う概念はあったのですが、最初生技の人の活動だったものをある時から製造の人たちに指導していくという形になったときに、「コマ図」と言われる絵を描くことをやってみたら、問題が起きている現場が特定されて、ここで問題が起こっているんじゃないかということが発見できるようになったのです。それを生産技術や技術者が見て、「こういう原理原則だね」という風に、協業していく今の(小集団)指導会の形が徐々にできていきました。
今ではここの加工点部分というのが、付帯良品条件、主要良品条件と言って言葉は難しいのですが、要するに生技の人が考えなければいけない良品条件と製造の人が維持管理しなければいけない良品条件というのが2種類ありまして、生産技術も製造も他人事じゃないと言う感じになっています。
JMAC:
製造の方が付帯良品条件、生産技術部門が主要良品条件を担う。言い換えればそれぞれ責任を持つことと言われていますね。
西雪:
はい。そういう考え方が当社にマッチしまして、要は生技だけの活動とか製造だけの活動とか、それぞれがうまい具合にいっているといったところです。簡単に歴史の方を話しましたが、そんな風にして現在に至っています。
2006年からPM分析教育を開始し、座学教育と事例づくり及び発表を年に2回ずつ行っています。当初は生産技術やスタッフを対象にスタートしましたが、PM指導員や製造工長、保全部門へと拡大していきました。
もともと技術者向けの取り組みだったのですが、PM分析のような考え方自体を現場に入れようというのが目的でした。
PM分析は、大学の講義のように数式や点で表す等とても難解です。ですが、現場の人は、見ているし知っていました。ただ、それを表現する手段がなかっただけでした。では見て実際に描いてみてくださいと言うと、描けるのです。不思議なもので異常のコマ図を最初に描いていたんですが、正常の図をつけると、そもそもの設備の原理原則とか、設備のことが調べやすくなったのです。
試行錯誤の中で、原理を知り、不具合の発生メカニズムを理解するために、加工点の正常と異常のGAPがどこのあるのか理屈で考える現在のフォーマットが誕生しました。
JMAC:
正しく現象を捉えて、発生の理屈を原理原則の観点から解明できるようにしたものが現在のコマ図になりますね。
西雪:
手描きで描いてやっていくと、設備のポイントがそこだとわかるので、周りに聞いたときに展開しやすくなりました。
最終的にはPM分析のように設備をしっかり調べると言うところまで落とし込まないと、結局対策にはつながりません。原理原則を理解し解析するPM分析の考え方と非常にマッチしたので、入れた当初の目的通りのことがやっとできるようになってきたと感じています。また、PM分析活動自体も事務局の考え方として、外部の先生に入っていただくことはとても効果があることだと思っています。同じ言われることでも、社内の人間から言われると現場も反発がありますが、外の先生からの指摘だと素直に耳を傾けてくれますので。
JMAC:
第三者を活用するメリットとして、我々も新たな刺激を提供するよう努めて参ります。
●人材育成を担当されている事務局メンバーとして、人材育成に関わるやりがいや苦労された点などについてお聞かせください。
西雪:
現場と関わる中で感じるのは、現場の人はとても元気がありますし、ものづくりと言うのは単純に見ていて面白いなということです。成果が上がることが我々のやりがいだと言いたいところですが、成果を上げるのは事務局ではなくて、現場の人たちです。だから現場の人たちが喜んで、成果が上がったことにやりがいを感じてもらえることが、私たちのやりがいではないでしょうか。なんとなく生き生きとした顔になってきた、この活動が面白いと思っていただけるのが一番ですね!
JMAC:
そのとおりですね。取り組みの中で特に苦労された点はありますか。
西雪:
製造現場の人たちにこういった科学的なことをやってもらうことが一番苦労した点でしょうか。私も入社した時から工場をターゲットに教育をしているのですが、もともと知識をお持ちの方にものを教えるわけです。それで試行錯誤しながら、最終的には「教えない」ということにたどり着きました。どうやってその人たちがもっている知識を引き出すのかという感じに、「コマ図」を描いてもらって、「こういうところがわかりづらい」とか、「こういう風に描いたほうがいい」と言った風に、教えるような感じでいながら逆に教えてもらっている。まさに引き出す形でやっていくようにしたのです。
JMAC:
考えさせる、考えてもらう、そして知識や知恵を引き出すという指導をされているわけですね。他に何かご苦労されている点はありますか。
西雪:
DXに関してでしょうか。具体的に何かといいますと、1番は社内と社外にいる時の格差です。今の時代、スマホ等で写真アプリだったり簡単にサーモグラフィー等も使えたりします。ですが一歩会社に入るとスマホを預けなければなりません。だから、いきなり何か10年ぐらい前にタイムスリップしているような感じになってしまって、会社の外と中でのギャップが苦労している点だと感じています。 それと今現場の人たちに対するアプローチの仕方が大分わかってきたのですが、最初はスタッフに対するアプローチに苦労していました。なぜスタッフ系が難しいかと言うと、先ほど申し上げたように、若干この活動が揚げ足取りのようなところがあるんですね。スタッフが作ってきたものに対してあれこれ指摘するわけですから。
JMAC:
より生産性の高いラインを入れるとか、設備を入れる、新しいシステムを入れると言うのは生産技術の役割です。そのためにも現状起きている問題点を次に持ち越さないとか、次に入れるときには、そういうものを加味した上で新しく導入することは不可欠ですからね。
西雪:
どうやったら前向きに捉えてもらえるか、良い言い回しがないかといつも考えています。
JMAC:
種々ご苦労やお気遣いされていらっしゃることに敬服いたします。
●アイシン様における「人材育成」の位置づけをお聞かせください。
JMAC:
我々と同じグループの一般社団法人日本能率協会が毎年企業経営者を対象に経営課題に関する実態調査を実施していますが、常に課題の上位にあがってくるのは人材育成です。最近ではDXも上位にあがっていますが、やはりいつの時代も人材育成・人づくりは多くの企業の重要課題となっています。
角谷:
当社では、人材育成は会社活動の基本、基盤と考え、これまで信念をもって取り組んできました。一言で「教育」と言うものの、どの教育にも実践が伴っていて、この実践を特に重視しています。和泉先生に教えていただいたことも、各現場で実践し、学んだことを自ら理解してやっていくことが大切だと思います。
JMAC:
机上で学び理解するだけではなく、実際に活用できてこそ、教育の価値があるわけですので。
角谷:
当社では「三現」といって、これは「現地・現物・現認」のことなのですが、それを実践してもらっています。
JMAC:
現場で起きていることや問題の本質を見出すには事実確認である。「三現」は大切なことですね。現場の人に納得してやっていただくためにいろんな仕掛けをされていると思いますが、特にどのようなご苦労があったでしょうか。
西雪:
一番困ったのは、ロスの最初の提言のところで「ロスをゼロにしなさい」と言うことでした。「〇〇不良ゼロ」と、最初それをそのまま言ってしまったので、現場のやる気をなくさせてしまったということがありましたね。
JMAC:
不良ゼロは競合に勝つためには避けて通れません。コンペチターのロスはわからないですが、自社のロスはわかるわけです。だから、もっともっとレベルをあげていきましょうと。そのためのアプローチの一つが、今回実施させていただいているPM分析教育ですね。
西雪:
このPM分析を通してブレークスルーだったのが、「ゼロになるまでロス発生の不具合現象を層別、分解する」という考えに現場の人がたどり着いたことです。そもそも〇〇不良というのはいろんな不良が重なり合って、実感としてそれがわからなかった。そこで、〇〇不良をゼロにできるまで分解していって、それをゼロにしてみると、成功体験につながったわけです。
JMAC:
現象を確実にゼロにし、再発させない仕組みを構築することが肝要です。
西雪:
本来苦労しているのは現場の人です。この活動をスムーズに受け入れてもらうために、外部の先生に入っていただいて、いわば先生の権威をお借りして、外部の力で推進していった感じです。
角谷:
例えば、次は外部の先生がいつ来られるから、その時までにここまで仕上げておこうといった風に動機付けできますから。そういった側面でも外部の支援と機会は大切です。
西雪:
最初、我々事務局がダイレクトに教えていた時は「何を言ってるんだ」という風な反発もありました。
JMAC:
外部の専門家がやった方がいいと言っているからと言えますしね。そこはうまく利用していただければと思います。それで実際に一つひとつのものがゼロになれば、現場の人もやって良かったと言う気持ちになりますし、腹落ちすれば次は自発的に動いてくれますよね。そこに到達するまでが一番の戦いですし、ご苦労される点だと思います。
西雪:
先ほど角谷が申しましたが、「三現」は基本中の基本です。ですが案外難しくて、ただ現場に出向いて行って「見ました」、「現地・現物・現認できました」と言えば済む話ではありません。形の上ではできたのかもしれませんが、その人の中で本来得られなければならないものが何だったんだろうと言う確証がもてなかったのです。そこで絵を描いてみようと。これは絵を描くのが上手い下手ではなくて、一番重要なのはわかっていないものは描けないと言うことです。うまく描けてその表現ができるということは、それはその人がちゃんとわかっているからですよね。形骸化はそれで乗り切れると思いました。
JMAC:
5W1Hで層別する、分けることは解る事ですし。ファクトファンディングが課題形成の第一歩で、そのためのスケッチです。
●貴社でPM指導員を配置した背景やその役割についてお聞かせください。
角谷:
当社ではPM指導員と呼んでいるのですが、社内資格のような位置づけでPM分析の指導員を認定する取り組みを行っています。具体的には、「TPMを自ら実践できる、現物・絵・数値で自職場の指導が出来る、良品条件に基づき、設備の異常を未然に検知し解決できる」といった役割です。
JMAC:
指導員と認定することで責任感を持ってもらえますね。
角谷:
旧アイシン精機の時には、各製造職場のすべての工長さん、係長クラスの人に、PM指導員になってもらうように取り組みまして、一時は約70名にも上りました。どの職場に行ってもPM分析の指導ができる人がいるという状態になりました。その後、アイシン精機とアイシン・エィ・ダブリュが統合したため、これを2024年には、100%にすると言う目標を立て、今まさに和泉先生にもお願いして取り組んでいるところです。
JMAC:
そうですね。アイシンさんは国内、海外、たくさん工場をお持ちです。PM指導員が現地でしっかり活躍してくれればそれは会社の成果にもつながります。実際PM指導員が海外赴任もされていますが、現地へ赴任された方々の状況はいかがでしょうか。
角谷:
アメリカでいろいろ工場を見て回ったのですが、こんな風にOEE(設備総合効率)を出しているんだと自ら説明してくれる現地の人もいました。話を聞くと、赴任者から教育実践を受け、グローバルにもTPMの考え方が普及してきました。
西雪:
先ほど角谷も話しましたが、実は現地の人たちもOEEというのは知っているんです。今までは注目を浴びてこなかったですが、日本から理解している人が来て話も合うし評価もしてくれるんだと。欧米系は保全について割としっかり勉強をしてやっているので、ずっとOEEをとっていたと実際に持ってきて見せてくれることもありましたね。
JMAC:
そのようにPM指導員が国内、海外で活躍してもらえればそれこそ推進部の狙い通りですね。
西雪:
100%とはいきませんが、確実に2割3割の人が工場等でも部下の指導で使ってくれたりしていると感じます。
JMAC:
今後はコマ図を含め海外現地法人でのPM指導員の養成と自立自走でしょうか。
西雪:
はい。今「コマ図」についてはまず社内で展開しようと思っているんですが、グループ会社でも教材を作りはじめているところです。これは今後の取り組みの一つですが、海外もさることながら、国内でも職場間で格差があるのは事実です。それぞれ職場の状況は異なりますが、やる事は一つ、思想も一つであるべきです。当社の中で良品条件と言う活動は、職場の全員参加という旗は下ろさずこれからも取り組んでいきたいと思います。
JMAC:
そうですね。企業は人で成り立っているわけですから。ぜひこれからの人材育成の取り組みに期待しています。
●最後に、JMACへ期待することがあればお聞かせください。
JMAC:
JMACでは、長年にわたりアイシン様にさまざまなご支援をさせていただいております。最後に、アイシン様から見た「JMACが提供する研修」の特徴や今後への期待などがありましたら、ぜひお聞かせください。
角谷:
JMACさんに期待していることの一つに、用語を正しく使うということがあります。社内教育においてはどうしても社内方言になりやすい、また知らないうちに用語の意味が変わってきたりしますよね。それは、他の会社の方と話すときに不便ですし、社内の中でも間違って理解されることがあったりします。
特にグローバル展開の時に失敗したことがありまして、5Sについても英語で訳していたのですが、後でローマ字で表現するのが一番だと聞きました。海外の文献等でもそういうものがちゃんと準備されているので、そういう風に使うのが一番間違いがないのだと。また、工長さんも社外の方に会う機会が多かったり、他の会社に出向される方もいるので、こういう風に社外の先生に教えていただくのが一番良いと言うことで、教育活動として継続してやっているという感じです。
JMAC:
なるほど。そういう側面もあったのですね。我々の支援の中で自主保全の教育をさせてもらっていることもありますし、TPM推進PlannigセミナーをはじめTPMカレッジ経営幹部コースもさせていただいております。それらが全て今後の貴社の人材育成につながっていくと良いですね。
角谷:
今も社内で流行りみたいになっているんですけれども、TPM推進Plannigセミナーでは部長クラスに教育していただきましたが、その時に学んだ「トレンド図」があちこちで浸透して活用されています。
JMAC:
将来のありたいイメージを具体化するということですね。
西雪:
あの研修は非常に人気があり、評判はとてもよかったです。
角谷:
ファンになった部長さんもたくさんいて、今も私たちの部署でもそうですし工場の指導会等を見に行っても、トレンド図が使われていて、役立っているなと感じます。
JMAC:
それはよかったです。今後もJMACの様々な支援がアイシンさんの教育体系に貢献できればうれしいです。まずは2024年のPM指導員100%配置を目標に、PM指導員講座を加速してまいりましょう。
本日はありがとうございました。